Por meio da aplicação de técnicas de machine learning, análise de dados operacionais e monitoramento preditivo da integridade de ativos, as equipes de engenharia podem simplificar a manutenção e reduzir os riscos relacionados à confiabilidade de ativos ou operações comerciais.
O uso de software específico para manutenção e como funciona a manutenção preventiva auxilia na garantia de operações estáveis, assegura a conformidade com garantias e soluciona problemas que afetam a produção antes que ocorram falhas. Implementar o monitoramento preditivo envolve os seguintes tipos de manutenção preventiva:
Manutenção Preventiva Baseada em Condição
Monitora continuamente as condições dos ativos por meio de sensores e outros dispositivos e intervém apenas quando os parâmetros estabelecidos indicam a necessidade de manutenção.
Manutenção Preventiva Baseada em Tempo
Nós estabelecemos um cronograma de manutenção regular, no qual nós realizamos intervenções em intervalos pré-determinados para evitar falhas.
Manutenção Preditiva
Utiliza técnicas avançadas de análise de dados para prever falhas em ativos e programar intervenções de manutenção antes que ocorram problemas.
Manutenção Prescritiva
A manutenção prescritiva mostra não apenas isso e quando as falhas ocorrerão, mas também as razões para elas. Este tipo de manutenção analisa e identifica várias opções e potenciais resultados para mitigar qualquer risco para a operação.
Manutenção Preventiva Baseada em Uso
Consideramos as horas de operação ou o uso dos ativos como base para agendar as intervenções de manutenção, garantindo que realizemos essas intervenções antes que ocorram falhas decorrentes do desgaste causado pelo uso.
Exemplos de manutenção preventiva
Na indústria, a manutenção periódica é essencial para garantir o pleno funcionamento da produção, além de prevenir prejuízos e atrasos causados por danos às máquinas. Dessa forma, o conceito de “manutenção preventiva” abrange uma variedade de tarefas obrigatórias e gerais. Para cada componente do sistema de produção, é necessário realizar algum tipo de manutenção regular. Além disso, é fundamental realizar a limpeza e lubrificação como cuidados mínimos para o equipamento. No entanto, em determinadas situações, pode ser necessário realizar uma manutenção mais abrangente, que envolve uma revisão detalhada, reparo ou até mesmo substituição de algumas peças.
Em um nível mais amplo, a manutenção preventiva também abrange a preservação das instalações físicas que abrigam os diversos sistemas de produção. As responsabilidades gerais dessa forma de manutenção preventiva incluem garantir o bom funcionamento dos sistemas de HVAC, verificar se todos os sistemas elétricos estão operando em conformidade com os padrões do código e assegurar que a iluminação necessária esteja funcionando corretamente.
Qual a diferença entre manutenção preventiva e preditiva?
Manutenção Preventiva
Frequentemente, há uma tendência de considerar a manutenção preventiva e a manutenção preditiva como áreas separadas. Infelizmente, essa comparação entre manutenção preventiva e preditiva ignora um fato importante. Na realidade, a manutenção preditiva é uma forma mais avançada de manutenção preventiva. Ambas as abordagens buscam antecipar e prevenir proativamente falhas na máquina. No entanto, a manutenção preditiva vai além.
Imagine um único dispositivo industrial. Normalmente, utilizamos informações gerais sobre a marca e o modelo da máquina na manutenção preventiva desse equipamento para fornecer uma estimativa aproximada de quando devemos realizar a manutenção programada.
Assim, sabemos quando executar a manutenção.
Manutenção Preditiva
Por outro lado, a manutenção preditiva é muito mais precisa e, portanto, requer uma quantidade maior de dados. Combinamos informações sobre o ciclo de vida esperado do modelo do dispositivo com dados históricos sobre o desempenho da unidade específica. Com esses dados adicionais, os modelos de manutenção preditiva são capazes de fornecer previsões precisas, permitindo que os operadores saibam com certeza quando ocorrerão as falhas do sistema.
Além disso, como os reparos planejados por meio da manutenção preditiva ocorrem pouco antes do tempo necessário, e não com base em um cronograma geral, evitam-se reparos desnecessários, o que impacta positivamente o orçamento de manutenção.
Com o auxílio da IoT, a manutenção preditiva se torna ainda mais eficiente. À medida que as máquinas geram continuamente atualizações sobre suas atividades e integridade, os modelos de manutenção preditiva obtêm os dados necessários para realizar as previsões de manutenção tão importantes.
Descubra uma solução de manutenção preditiva.
Benefícios da manutenção preventiva
Ao adotar uma estratégia de manutenção preventiva, você obtém benefícios máximos de seus ativos e reduz custos. Além disso, há outras vantagens, como maior organização e disponibilidade operacional contínua.
Estende o ciclo de vida do ativo
Podemos planejar as atividades de manutenção e inspeções de forma sistemática, com o objetivo de garantir que seus ativos alcancem seu ciclo de vida completo e mantenham as garantias atualizadas. Isso proporciona benefícios significativos, incluindo maior longevidade dos ativos e garantia de conformidade com os termos de garantia.
Reduz as necessidades de manutenção
Ao gerenciar tanto a manutenção planejada quanto a não planejada, bem como o estoque e os custos de peças de reposição, é possível obter uma visão mais precisa dos processos e ativos. Essa abordagem, por sua vez, auxilia na redução significativa dos custos de manutenção. Além disso, permite um controle mais eficiente dos recursos, evitando gastos desnecessários e, ao mesmo tempo, assegurando a disponibilidade adequada de peças de reposição quando necessário.
Aumenta a produtividade
Uma força de trabalho bem-organizada é mais produtiva. Além disso, um software aprimora o planejamento, o gerenciamento de fornecedores e o fluxo de trabalho, ao mesmo tempo em que oferece relatórios financeiros sem a necessidade de papel. Essa combinação resulta em maior eficiência operacional, redução de erros e agilidade na tomada de decisões.
Reduz o tempo de inatividade não planejado
Identificamos precocemente os reparos requeridos durante o ciclo de vida de um ativo. Dessa forma, consequentemente, resulta em processos operacionais altamente disponíveis, além da redução do tempo de inatividade e otimização da produção.
Como a manutenção preventiva é diferente da manutenção corretiva?
Existe uma diferença essencial entre a manutenção preventiva e a manutenção corretiva: o tempo. A abordagem da manutenção corretiva baseia-se em tomar medidas de manutenção apenas quando um componente do dispositivo não está mais funcionando. Em seguida, devemos fazer o reparo necessário o mais rápido possível. Por outro lado, a manutenção preventiva visa antecipar falhas no equipamento e tomar medidas corretivas antes que ocorram danos à máquina.
A escolha entre os métodos – manutenção preventiva ou manutenção corretiva – é importante, pois a manutenção corretiva pode se tornar rapidamente muito mais cara do que a manutenção preventiva. Todos nós sabemos disso em relação à manutenção de carros.
Se um carro não passar regularmente pelas inspeções necessárias, há um alto risco de ocorrer uma falha catastrófica em vários sistemas e, de repente, ser necessária uma reparação extensa e cara.
Embora as medidas de manutenção preventiva exijam planejamento para inspeções regulares e possivelmente a implementação de um sistema computadorizado de gerenciamento de manutenção (CMMS), geralmente vale a pena em um ambiente industrial.
Isso ocorre porque, quando interrompemos uma operação industrial devido a reparos não planejados, isso pode rapidamente levar a interrupções na produção ou até mesmo à perda de vendas.
O futuro da manutenção preventiva com IA e IoT
A implementação de tecnologias de IA e IoT está levando a uma otimização contínua tanto dos ativos quanto das atividades no setor industrial. Além disso, ao considerar o futuro da manutenção preventiva, torna-se evidente que o uso de monitoramento remoto e modelagem analítica já resultou em uma redução líquida nos recursos dedicados à execução de tarefas de manutenção preventiva.
Do ponto de vista da fábrica, os fabricantes podem obter dados valiosos que aprimoram a confiabilidade das operações e dos produtos, graças à coleta e análise abrangente de dados. Por conseguinte, isso é possível devido às modernas soluções de IA e IoT. Além disso, os operadores de ativos podem compreender verdadeiramente a qualidade dos ativos implantados para as operações e desenvolver novas estratégias para seu ciclo de vida. Assim, sistemas de baixo desempenho podem ser retirados de operação, e falhas e custos podem ser reduzidos. Descubra como a EAM móvel oferece suporte ao gerenciamento de serviços de campo.
Soluções semelhantes para manutenção de instalações
Soluções semelhantes para manutenção de instalações incluem:
- Manutenção preditiva: Utilizando tecnologias avançadas, como sensores e análise de dados, é possível prever falhas e realizar manutenção antes que ocorram problemas graves. Isso reduz o tempo de inatividade e os custos associados.
- Manutenção preventiva: Realizando inspeções regulares e manutenção programada com base em recomendações do fabricante, é possível evitar falhas e maximizar a vida útil dos equipamentos e instalações.
- Manutenção corretiva: Realiza-se ações de reparo e substituição de componentes somente quando ocorrem falhas ou danos. Embora seja uma abordagem reativa, ainda é necessária para resolver problemas imprevistos.
- Gerenciamento de ativos: Utilizando sistemas de gerenciamento de ativos, é possível rastrear e monitorar o desempenho de equipamentos e instalações, agendar manutenções, controlar estoques de peças e otimizar os recursos disponíveis.
- Automação e IoT: Integrar sistemas de automação e Internet das Coisas (IoT) pode permitir o monitoramento em tempo real, o controle remoto e a coleta de dados em tempo real para melhorar a eficiência e a tomada de decisões na manutenção de instalações.
Essas soluções visam maximizar a disponibilidade e a confiabilidade das instalações, reduzir os custos de manutenção e melhorar a eficiência operacional. A escolha da solução mais adequada depende das necessidades específicas de cada instalação e dos objetivos de manutenção estabelecidos.
Recursos de manutenção Preventiva
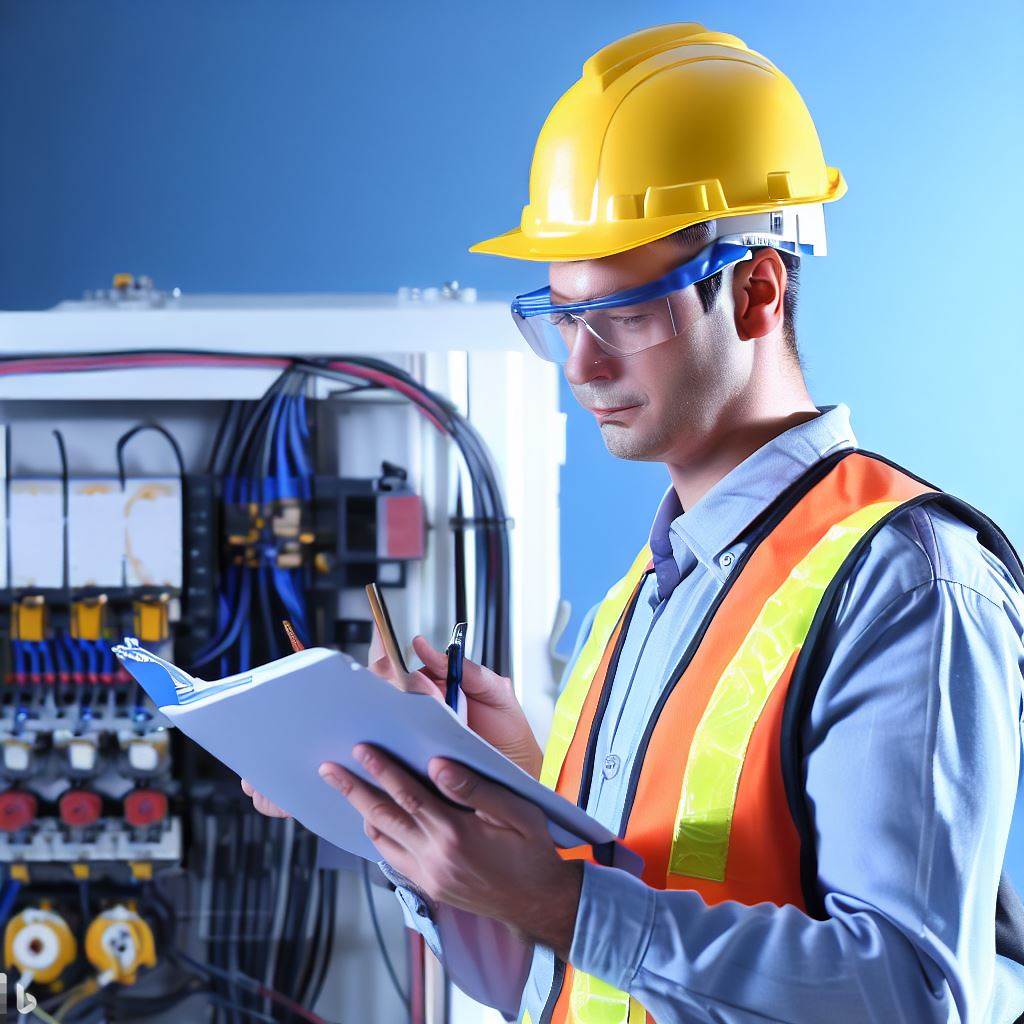
Como a manutenção preditiva melhora a eficiência em todos os setores
A IFELL auxilia empresas de todos os segmentos a implementarem a manutenção preditiva visando aprimorar seu rendimento. Além disso, clique aqui para conferir cinco casos de clientes que ilustram como a manutenção preditiva em nuvem está impulsionando o sucesso de empresas em cinco setores distintos.
Por que algumas empresas estão mais bem preparadas para disrupções do que outras?
Existem várias razões pelas quais algumas empresas estão mais bem preparadas para disrupções do que outras. Abaixo estão alguns pontos a serem considerados:
Visão estratégica:
Por um lado, empresas que possuem uma visão estratégica de longo prazo estão mais preparadas para enfrentar disrupções. Por outro lado, elas antecipam mudanças no mercado e investem em tecnologias e soluções de manutenção que ajudam a garantir a continuidade dos negócios.
Resiliência operacional:
Além disso, empresas que têm uma cultura de resiliência operacional estão mais preparadas para lidar com disrupções. Por exemplo, elas possuem planos de contingência e processos bem definidos para lidar com situações imprevistas, garantindo a continuidade das operações mesmo diante de desafios.
Investimento em tecnologia:
Além disso, empresas que investem em tecnologias avançadas, como manutenção preditiva e IoT, estão mais bem preparadas para enfrentar disrupções. Portanto, essas tecnologias permitem o monitoramento contínuo de ativos, identificação precoce de problemas e tomada de decisões mais informadas, reduzindo o risco de falhas e tempo de inatividade não planejado.
Equipe qualificada:
Por fim, empresas que contam com equipes de engenharia qualificadas e atualizadas estão mais preparadas para lidar com disrupções. Portanto, essas equipes possuem conhecimento técnico, experiência e habilidades necessárias para implementar e utilizar corretamente as tecnologias de manutenção, garantindo a continuidade dos negócios.
Em resumo, empresas que possuem uma visão estratégica, investem em tecnologia, possuem resiliência operacional e equipes qualificadas estão mais bem preparadas para enfrentar disrupções. Além disso, ao adotar as tecnologias de manutenção corretas e garantir a continuidade dos negócios, as equipes de engenharia desempenham um papel fundamental na preparação e resposta eficaz a disrupções.
O teste de sistemas elétricos é obrigatório
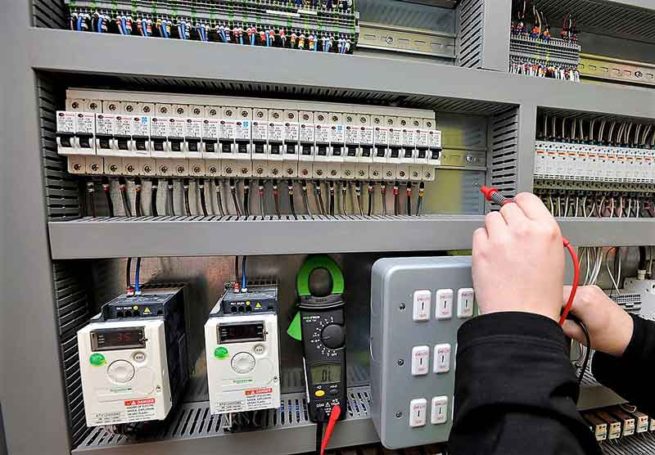
Muitas empresas optam pela resolução de problemas em vez da manutenção preventiva e reparo de seus sistemas elétricos. As empresas justificam isso pela economia de custos, como evitar a contratação de um eletricista próprio. No entanto, com essa abordagem, elas arriscam a segurança elétrica durante a operação e não economizam custos a longo prazo. Descubra aqui por que economizar custos ao testar sistemas e equipamentos elétricos não é vantajoso.
Os sistemas elétricos, independentemente de serem novos ou antigos, estão em constante evolução durante a operação normal. Intervenções externas podem provocar alterações eletrotécnicas de forma ativa, mas elas também podem ocorrer de forma passiva a qualquer momento durante a operação normal, como processos de comutação e controle ou sobrecargas breves.
Manutenção e teste de sistemas elétricos é uma obrigação
Os sistemas elétricos requerem a manutenção e testes realizados por profissionais em intervalos regulares. Somente os sistemas elétricos com manutenção e testes profissionais oferecem o mais alto nível de segurança operacional, garantindo assim a proteção pessoal, patrimonial e contra incêndios mais elevada.
Normas e Regulamentos
- ABNT NBR ISO 9001:2015 – Sistema de gestão da qualidade – Requisitos: Esta norma estabelece os requisitos para um sistema de gestão da qualidade, que inclui a manutenção preventiva como parte integrante da melhoria contínua dos processos.
- ABNT NBR 5462:1994 – Manutenção preventiva – Procedimento: Esta norma estabelece os princípios e procedimentos para a execução da manutenção preventiva em equipamentos e instalações.
- ABNT NBR 5461:1994 – Manutenção preventiva – Terminologia: Esta norma define os termos relacionados à manutenção preventiva, fornecendo um vocabulário padronizado para uso nesse contexto.
- ABNT NBR 14039:2005 – Instalações elétricas de média tensão de 1,0 kV a 36,2 kV: Esta norma estabelece os requisitos para instalações elétricas de média tensão e inclui diretrizes para a manutenção preventiva dessas instalações.
- ABNT NBR 5410:2004 – Instalações elétricas de baixa tensão: Esta norma especifica as condições exigíveis para projetos, execução e manutenção de instalações elétricas de baixa tensão, incluindo recomendações para a manutenção preventiva.
Inspeção de sistemas elétricos: Eletricista é necessário
Qualificação e treinamento: Requisitos para trabalhar com segurança em sistemas elétricos de potência
Para fazer uma declaração tecnicamente precisa sobre a condição de um sistema elétrico, é importante que a pessoa seja qualificada como eletricista de acordo com o treinamento estabelecido na norma NR-10 SEP (Segurança em Instalações e Serviços em Eletricidade). Além disso, essa norma estabelece os requisitos para garantir a segurança das pessoas que trabalham na área de engenharia elétrica. Ademais, o grupo de pessoas qualificadas inclui profissionais como engenheiros eletricistas, que possuem o mais alto nível de conhecimento técnico, e especialistas em eletricidade.
Por outro lado, o Sistema Elétrico de Potência (SEP) é uma estrutura composta por elementos e equipamentos de geração, transmissão e distribuição de energia elétrica em alta tensão. Além disso, esses sistemas são responsáveis por garantir o fornecimento de energia elétrica de forma confiável, eficiente e segura para atender às demandas das diversas instalações e consumidores.
No contexto da segurança elétrica, o SEP apresenta características específicas que exigem cuidados e medidas de proteção adicionais. Portanto, o trabalho em um SEP requer conhecimentos técnicos especializados, habilidades e treinamentos específicos para lidar com os riscos associados a altas tensões e correntes elétricas.
Norma NR-10 e sua importância na segurança do SEP: Diretrizes e responsabilidades para evitar acidentes elétricos
Por sua vez, a norma regulamentadora NR-10, em sua abordagem específica para o SEP, estabelece diretrizes e requisitos para garantir a segurança dos trabalhadores que atuam nesse sistema. Assim, ela define as responsabilidades dos empregadores e dos trabalhadores, exigindo a implementação de medidas de prevenção de acidentes elétricos, como o uso de equipamentos de proteção individual e coletiva, a realização de análises de risco, o cumprimento das normas técnicas aplicáveis e a capacitação adequada dos profissionais envolvidos.
A aplicação correta da NR-10 no contexto do SEP é fundamental para evitar acidentes graves, choques elétricos, curtos-circuitos e incêndios. Nesse sentido, é essencial que as empresas do setor elétrico e os profissionais que atuam nesse ambiente estejam devidamente capacitados e sigam as diretrizes estabelecidas pela norma, garantindo assim a segurança operacional e a integridade dos trabalhadores e do próprio sistema elétrico de potência.
Manutenção preventiva e medidas de reparo versus solução de problemas
Surpreendentemente, a experiência tem demonstrado que, em contraste com as empresas administradas comercialmente, as empresas administradas tecnicamente são, em média, mais confiáveis em relação à engenharia elétrica e, consequentemente, mais resilientes a danos por incêndio relacionados à engenharia elétrica.
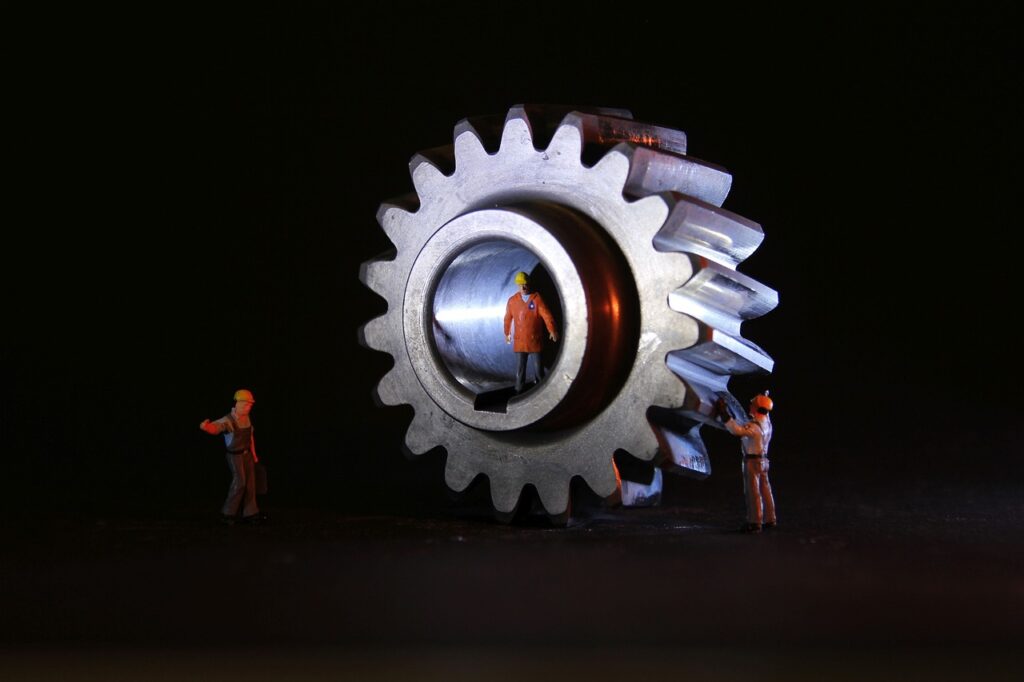
Empresas predominantemente comerciais costumam focar apenas na solução de problemas em seus sistemas elétricos e empresas externas de eletricidade realizam esses trabalhos. Por outro lado, as empresas com gestão técnica geralmente possuem um departamento elétrico próprio que realiza a manutenção preventiva e os reparos em seus sistemas elétricos.
Essa é uma decisão clara sob o ponto de vista comercial. Ter um eletricista interno implica em custos durante os 365 dias do ano, enquanto a contratação de um eletricista externo temporário, como parte de um serviço, gera custos baseados apenas no esforço real necessário.
No entanto, do ponto de vista eletrotécnico, esse cálculo é falacioso. Se profissionais não realizarem manutenção e reparos com profissionalismo, os custos do sistema elétrico aumentam desproporcionalmente a cada ano, pois falhas e erros ocorrem com cada vez mais frequência. Se tudo precisar ser feito às pressas para manter a produção, isso geralmente resulta em medidas provisórias arriscadas em termos de incêndios e acidentes.
Testes iniciais e repetidos de sistemas elétricos
Existem várias normas brasileiras que abordam os testes iniciais e repetidos de sistemas elétricos, com o objetivo de garantir a segurança e o desempenho adequado desses sistemas. A seguir, apresento alguns artigos de normas relevantes:
NBR 5410 – Instalações elétricas de baixa tensão:
Artigo 6.4.1: Estabelece a necessidade de testes de continuidade e resistência de condutores elétricos em instalações.
Artigo 7.1.3: Determina a realização de testes de funcionamento e desempenho dos dispositivos de proteção, como disjuntores e fusíveis.
NBR 14039 – Instalações elétricas de média tensão de 1,0 kV a 36,2 kV:
- Artigo 6.4.2: Estabelece a obrigatoriedade de testes de resistência de isolamento e continuidade dos circuitos elétricos.
- Artigo 7.2.2: Determina a realização de testes de funcionamento e desempenho dos dispositivos de proteção.
NBR 5419 – Proteção contra descargas atmosféricas:
- Artigo 10.2.2: Estabelece a necessidade de testes de continuidade e resistência de aterramento das instalações elétricas para proteção contra descargas atmosféricas.
NR 10 – Segurança em instalações e serviços em eletricidade:
- Artigo 10.3.5: Determina que as instalações elétricas devem ser submetidas a testes, inspeções e manutenções periódicas, de acordo com as prescrições das normas técnicas vigentes.
Essas são apenas algumas das normas brasileiras relevantes que mencionam os testes iniciais e repetidos de sistemas elétricos.
Profissionais qualificados devem aplicar essas normas em conformidade com as diretrizes específicas de cada norma para garantir a segurança e o desempenho adequado dos sistemas elétricos.
De acordo com a NBR 5410, durante o teste inicial, ou seja, quando é recém-instalado ou após uma grande mudança, deve-se testar todo sistema elétrico durante a instalação e após a conclusão, na medida do possível, antes de colocá-lo em operação pelo usuário.
Não existe um período de teste claramente definido para a realização de testes periódicos em sistemas elétricos. É responsabilidade do operador determinar os intervalos apropriados de teste, levando em consideração sua avaliação de risco específica.
O operador do sistema elétrico deve definir os períodos de teste adequados e o escopo dos testes, considerando as condições de operação, a fim de realizar uma avaliação precisa da condição dos sistemas elétricos.
No entanto, essa responsabilidade própria do operador dos sistemas elétricos representa uma fraqueza significativa na prática. Infelizmente, argumentos econômicos superficiais ou falta de conhecimento profissional ou técnico levaram a administração de empresas industriais a interpretar esse escopo discricionário de forma inadequada ou negligente, resultando em intervalos de teste muito longos ou até mesmo sua não realização.
Teste obrigatório de acordo com NBR 5410 para testar sistemas e equipamentos elétricos
Conforme estabelecido pela norma NBR 5410, é obrigatório realizar testes em sistemas e equipamentos elétricos. Esses testes têm o objetivo de garantir a conformidade e segurança dos sistemas elétricos, de acordo com as diretrizes estabelecidas.
A NBR 5410 especifica os procedimentos e critérios para realizar os testes necessários, que incluem testes de continuidade, resistência de isolamento, funcionamento e proteção dos dispositivos de segurança, entre outros.
Esses testes são fundamentais para verificar a adequação dos sistemas e equipamentos elétricos, garantindo que estejam em conformidade com os requisitos técnicos e normativos estabelecidos. Além disso, contribuem para a prevenção de acidentes elétricos e garantem o bom funcionamento e desempenho dos sistemas elétricos.
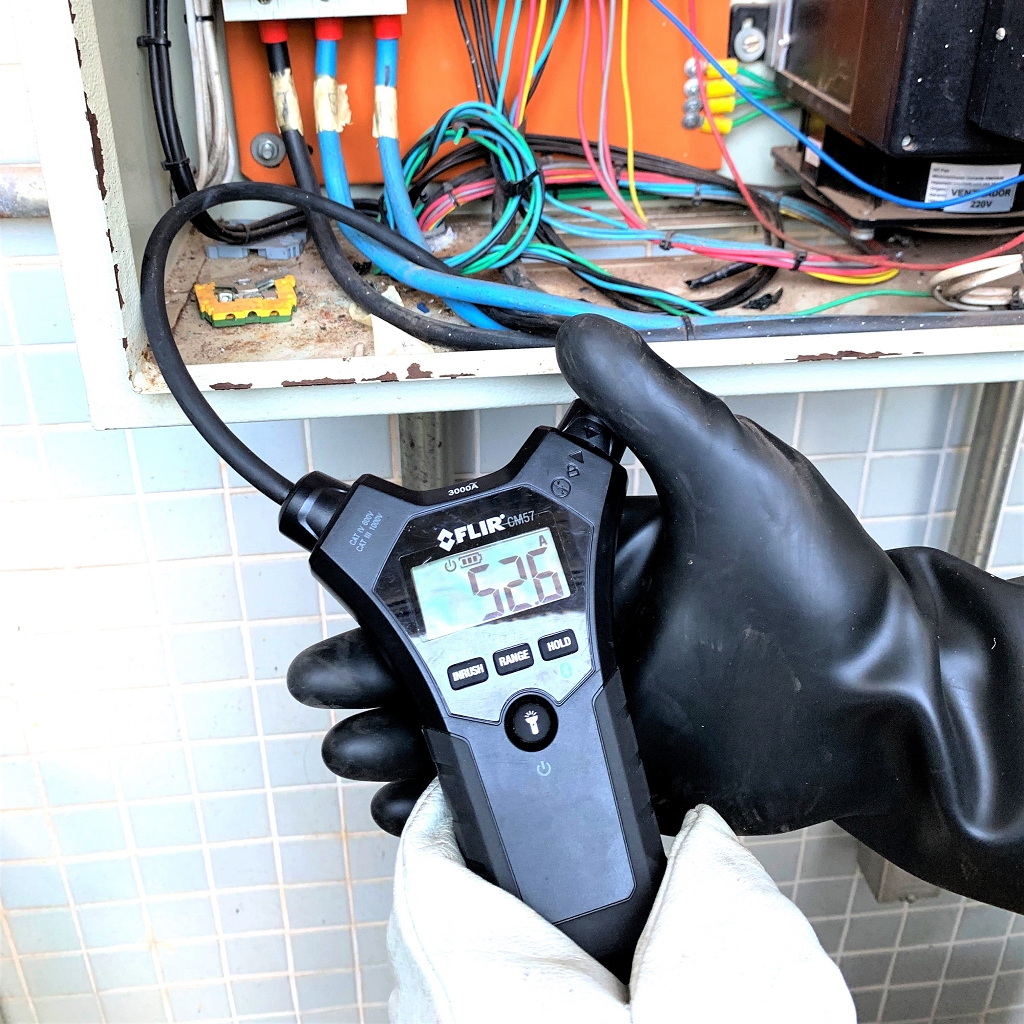
Dentre os testes exigidos pela norma NBR 5410 para sistemas e equipamentos elétricos, destacam-se os seguintes:
Teste de Continuidade
Esse teste consiste em verificar a existência de uma conexão contínua e eficiente em condutores e circuitos elétricos. É realizado por meio da medição da resistência elétrica, garantindo que não haja interrupções ou falhas na passagem da corrente elétrica.
Teste de Resistência de Isolamento:
Esse teste avalia a resistência do isolamento entre condutores ativos e terra, bem como entre condutores ativos de diferentes circuitos. O objetivo é verificar se o isolamento elétrico está adequado, prevenindo riscos de curto-circuito, choques elétricos e danos aos equipamentos.
Teste de Funcionamento dos Dispositivos de Proteção:
Nesse teste, verifica-se o correto funcionamento dos dispositivos de proteção, como disjuntores, fusíveis, dispositivos de corrente residual (DR), entre outros. É importante assegurar que esses dispositivos atuem de maneira eficiente, desligando o circuito elétrico em caso de sobrecarga, curto-circuito ou falhas de isolamento.
Teste de Verificação de Polos:
Esse teste é realizado em interruptores, tomadas e outros dispositivos para garantir a correta conexão dos condutores elétricos. Verifica-se se os polos (fases) estão corretamente conectados e identificados de acordo com as normas de cores.
Teste de Funcionamento de Equipamentos Elétricos:
Esse teste avalia o desempenho e funcionamento de equipamentos elétricos, como motores, lâmpadas, transformadores, entre outros. Verifica-se se estão operando de acordo com as especificações técnicas e se não apresentam falhas que possam comprometer sua segurança e eficiência.
A manutenção preventiva e os reparos evitam avarias dispendiosas
Muitas ocorrências e falhas operacionais podem ser evitadas por meio da implementação de medidas preventivas. Cada vez mais, proprietários e operadores de sistemas elétricos estão confirmando essa realidade. As interrupções não planejadas nos negócios e as perdas de produção estão associadas a custos significativos. Na manutenção preventiva, a limpeza e organização das instalações são frequentemente negligenciadas em favor de dispositivos caros de inspeção.
Em diversas empresas, só se abrem e verificam os sistemas elétricos, especialmente os quadros de distribuição e os distribuidores, em casos de falhas. As rotas dos cabos e os poços de instalação também não são inspecionados e avaliados há anos. No caso das rotas dos cabos e poços de instalação, a acumulação de poeira, entulho ou líquidos pode afetar negativamente as instalações. Esses depósitos podem levar ao aumento de calor e os cabos podem aquecer. Defeitos de isolamento não são detectados e roedores causam danos, principalmente quando há presença de ração em pó. Em empresas com depósitos de poeira, a limpeza e manutenção das rotas dos cabos são tarefas essenciais e econômicas.
A poluição é comum
Infelizmente, mesmo com instalações novas, as vias e os cabos não recebem a devida limpeza, e os resíduos permanecem nas instalações por longos períodos. No caso de dispositivos de comutação e pontos de controle nos sistemas elétricos, o acúmulo de sujeira e poeira tem um impacto negativo mais rápido. A poeira fina penetra nos interruptores e dispositivos de comutação por meio de pequenas rachaduras. Quem não está familiarizado com o zumbido dos contatos nos sistemas de distribuição elétrica? A poeira entre a armadura e o garfo impede um encaixe adequado do contato, resultando no zumbido do contato. A presença de poeira nos contatos causa “contatos soltos” ou até mesmo queima devido ao calor gerado pelos arcos durante as operações de comutação. Isso leva à deterioração parcial dos contatos. A quantidade de poeira na caixa pode ser reduzida por meio de vedação adequada e proteção IP, juntamente com outras medidas preventivas.
Limpeza cuidadosa essencial
Em muitas empresas, utiliza-se ar comprimido para remover a poeira das instalações. No entanto, é importante observar que a poeira não é coletada, apenas redistribuída de maneira diferente. Na pior das hipóteses, sopra-se mais poeira nos componentes elétricos do que já está presente neles. Além disso, os funcionários ficam expostos à poeira suspensa, o que pode ser desagradável e prejudicial à saúde. Por outro lado, a aspiração é muito mais eficaz na remoção da poeira. Ao utilizar um aspirador, as partículas de poeira são retidas no próprio aparelho e podem ser posteriormente descartadas adequadamente. É importante utilizar um aspirador eficiente para que as partículas de poeira sejam aspiradas das rachaduras finas dos painéis e das várias camadas dos cabos.
O que é um bom aspirador?
Potência elétrica versus desempenho do aspirador: Entenda a relação
A potência elétrica elevada do aspirador é frequentemente anunciada. No entanto, essa informação não está diretamente relacionada ao desempenho do aparelho. Os aspiradores eficientes de hoje possuem uma alta capacidade de sucção de poeira com um consumo de energia relativamente baixo. A tecnologia do filtro e o direcionamento do fluxo de ar são extremamente importantes para a eficácia do aspirador. Você pode comparar os dados das diferentes descrições de produtos nesse aspecto. Para garantir um desempenho consistente ao longo do tempo, é fundamental limpar o filtro da maneira mais fácil e conveniente possível no dia a dia.
Facilidade de limpeza do filtro: Garantindo um desempenho consistente ao longo do tempo
No meu trabalho, também necessito dos acessórios adequados para lidar de forma ideal com várias tarefas. Em caso de muita poeira, use um recipiente maior no aspirador para usá-lo por mais tempo sem esvaziá-lo sempre. No entanto, devido ao tamanho e peso maiores do recipiente, o aspirador pode se tornar menos prático. O recipiente de pó deve ser fácil de esvaziar e limpar para que o aspirador possa ser rapidamente utilizado. Assim como em muitas tarefas, o uso da ferramenta certa no local certo leva ao melhor resultado possível.
Aspiradores para poeira perigosa da classe H: Requisitos especiais e certificação para trabalhos com amianto
Os aspiradores adquiridos para aspirar poeira perigosa da classe H, com requisitos adicionais para amianto, exigem atenção especial. Esses aspiradores só podem ser utilizados em trabalhos relacionados ao amianto. O fabricante desses dispositivos certifica, por meio de uma declaração de conformidade, que o aspirador é adequado para trabalhar com amianto. Devido ao alto custo de uso e manutenção de aspiradores para substâncias perigosas, especialmente o amianto, é aconselhável alugar o aspirador quando necessário. Segundo a norma IEC-EN 60335-2-69, os dispositivos devem passar por uma inspeção anual pelo fabricante ou especialista autorizado, com registro obrigatório. Empresas de remoção de amianto ou fornecedores de equipamentos oferecem esse serviço.
FAQ
1. Quais são os principais benefícios da manutenção preventiva?
Ela oferece diversos benefícios, como redução de custos, aumento da vida útil dos equipamentos, maior eficiência operacional e minimização de paralisações não programadas.
2. Qual é a diferença entre manutenção preventiva e corretiva?
Ela é realizada antes de ocorrerem falhas, com o objetivo de evitar problemas. Já a manutenção corretiva é realizada após uma falha, com o objetivo de reparar o equipamento.
3. Como definir os intervalos de manutenção preventiva?
Os intervalos de manutenção devem ser determinados com base nas recomendações dos fabricantes, nas condições de operação e nas características específicas de cada equipamento.
4. Quais são as ferramentas úteis para a implementação da manutenção preventiva?
Algumas ferramentas úteis incluem software de gerenciamento de manutenção, sensores e dispositivos de monitoramento.
5. É realmente necessário seguir um plano de manutenção preventiva?
Sim, um plano é essencial para estabelecer diretrizes, definir as tarefas a serem realizadas e garantir que a manutenção seja realizada de forma consistente e adequada.
6. O que é manutenção preventiva?
R: Sem dúvida, a manutenção preventiva refere-se a ações programadas e sistemáticas para cuidar e monitorar equipamentos e sistemas. Seu objetivo principal é prevenir falhas e garantir o funcionamento eficiente e seguro dos dispositivos.
7. Qual a diferença entre manutenção preventiva e corretiva?
R: De fato, enquanto a preventiva é focada em prevenir falhas por meio de verificações regulares, a corretiva trata dos problemas após sua ocorrência, corrigindo defeitos e restaurando a funcionalidade do equipamento.
8. Por que a manutenção preventiva é importante?
R: Sem dúvida, a preventiva é crucial para garantir a confiabilidade, eficiência e longevidade dos equipamentos, minimizando paralisações e reduzindo custos a longo prazo.
9. A manutenção preventiva pode economizar dinheiro?
R: Sem dúvida, ao evitar falhas inesperadas e caras reparações, a preventiva pode resultar em economias significativas para as empresas a longo prazo.
10. Quão frequentemente a manutenção preventiva deve ser realizada?
R: Naturalmente, a frequência varia dependendo do equipamento ou sistema em questão. É essencial consultar manuais e especialistas para determinar o cronograma ideal.
11. Quem deve realizar a manutenção preventiva?
R: Geralmente, técnicos especializados e treinados são os mais indicados para executar tarefas de manutenção preventiva, garantindo eficácia e segurança.
12. A manutenção preventiva garante que os equipamentos nunca falhem?
R: Embora a manutenção reduza significativamente o risco de falhas, não há garantias absolutas. Contudo, ela aumenta consideravelmente a confiabilidade do equipamento.
13. Qual é o impacto da manutenção preventiva na segurança?
R: Notavelmente, ao identificar e corrigir problemas potenciais, a preventiva aumenta a segurança dos operadores e do ambiente de trabalho.
14. A manutenção preventiva é aplicável a todos os tipos de equipamentos?
R: Certamente, enquanto a abordagem específica pode variar, a preventiva é benéfica para quase todos os tipos de equipamentos e sistemas.
15. Como a manutenção preventiva afeta a vida útil do equipamento?
R: De fato, ao manter o equipamento em ótimo estado, a preventiva pode prolongar significativamente sua vida útil.
16. A manutenção preventiva é uma prática sustentável?
R: Certamente, equipamentos bem mantidos tendem a consumir menos energia e recursos, promovendo práticas mais sustentáveis.
17. Quais são os primeiros passos para implementar uma estratégia de manutenção preventiva?
R: Primeiramente, é vital realizar uma avaliação detalhada dos equipamentos, definir prioridades e estabelecer um cronograma regular de inspeções e manutenções.
18. A manutenção preventiva requer treinamento especializado?
R: Sim, de fato, para garantir a eficácia da manutenção, é essencial que os técnicos recebam treinamento adequado.
19. Como a manutenção preventiva afeta a produtividade?
R: Sem dúvida, ao minimizar paralisações e garantir o desempenho eficiente do equipamento, a manutenção preventiva pode melhorar significativamente a produtividade.
20. Existem softwares ou ferramentas específicas para ajudar na manutenção preventiva?
R: De fato, existem várias soluções de software disponíveis que auxiliam na programação, monitoramento e documentação das tarefas de manutenção.
21. Como posso medir o ROI (Retorno sobre o Investimento) da manutenção preventiva?
R: Com efeito, comparando os custos associados à manutenção com as economias resultantes de menos falhas, maior vida útil do equipamento e eficiência operacional, você pode calcular o ROI.
22. A manutenção preventiva é a mesma em diferentes indústrias?
R: Embora o conceito seja universal, as práticas específicas e a frequência podem variar amplamente dependendo da indústria e do tipo de equipamento.
23. A manutenção preventiva pode ser terceirizada?
R: Sem dúvida, muitas empresas optam por terceirizar suas necessidades de manutenção para especialistas externos.
24. O que é um plano de manutenção preventiva?
R: De fato, é um cronograma estruturado que detalha quando e como as tarefas de manutenção devem ser realizadas.
25. Como a manutenção preventiva se relaciona com a manutenção preditiva?
R: Enquanto a preventiva é baseada em cronogramas, a preditiva, por outro lado, depende da condição real do equipamento, usando monitoramento e análises para determinar necessidades.
26. Quais são os desafios na implementação da manutenção preventiva?
R: Certamente, os desafios incluem custos iniciais, treinamento de pessoal e a necessidade de mudança cultural para priorizar a prevenção.
ENTRAR EM CONTATO